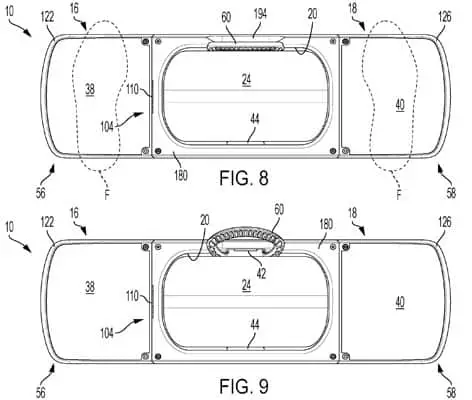
Onewheels seem like something out of a Sci-Fi movie. The Onewheel is a self-balancing electric skateboard that basically utilizes a combination of gyroscopes and accelerometers to maintain balance and stability for the rider. Onewheels are made of these elements: the frame (rails), foot pads (one is a sensor), controller box (which houses a controller that has accelerometers and gyroscopes), battery box (which houses the battery and battery management system [BMS]), and the hub motor assembly (stator, rotor, hall sensors). Here’s a detailed explanation of how these components work together:
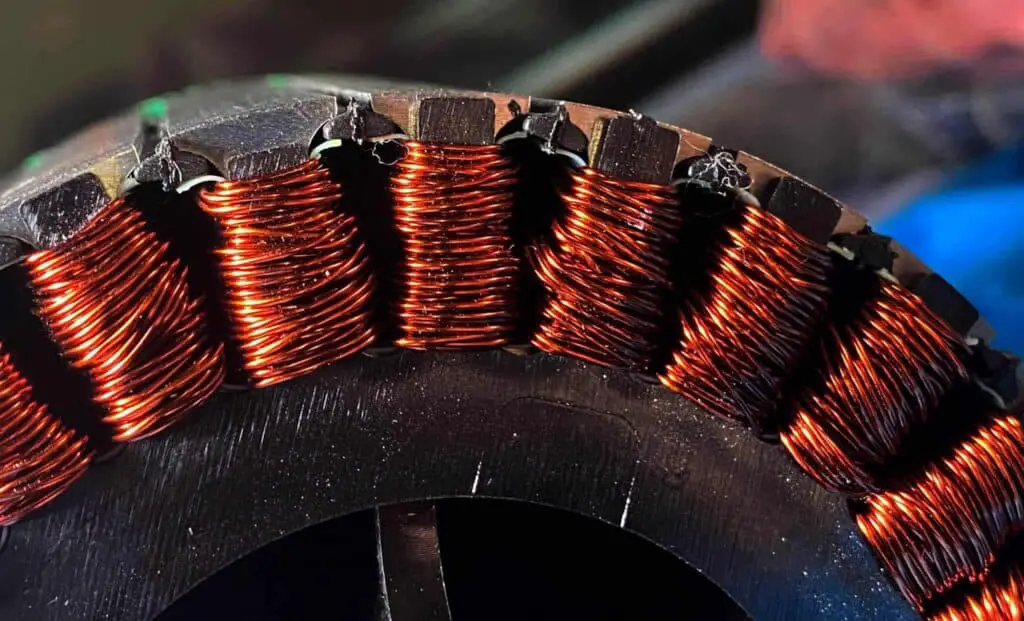
The Controller Box
The controller box houses the brains of the Onewheel. Within the box are accelerometers and gyroscopes that communicate to the the motor assembly and are powered by the lithium-ion battery. Lets review what each component does:
Onewheel Gyroscopes
Gyroscopes are sensors that measure the rotational movement or orientation of an object. In the case of the Onewheel, there are multiple gyroscopes strategically placed within the board’s controller box. These gyroscopes continuously detect any tilting or leaning motions of the board in relation to the rider.
When the rider leans forward or backward, the gyroscopes detect the change in orientation and provide feedback to the control system. This information is crucial for maintaining balance and stability during the ride. There is constant communication between the controller and with the BMS as you are kept balanced.
Accelerometers:
Accelerometers are sensors that measure linear acceleration or changes in velocity. Similar to the gyroscopes, the Onewheel has accelerometers to detect the acceleration and/or deceleration of the rider.
When the rider accelerates or decelerates, the accelerometers detect the change in velocity and transmit this data to the control system. This is always grabbing the correct power from the battery. This allows the Onewheel to adjust the motor’s power output accordingly, ensuring a smooth and controlled riding experience.
Control System as a Unit:
The gyroscopes and accelerometers work in conjunction with the Onewheel’s controller which processes the data received from these sensors in real-time. The control system uses complex algorithms to analyze the sensor inputs and make instant adjustments to the motor output.
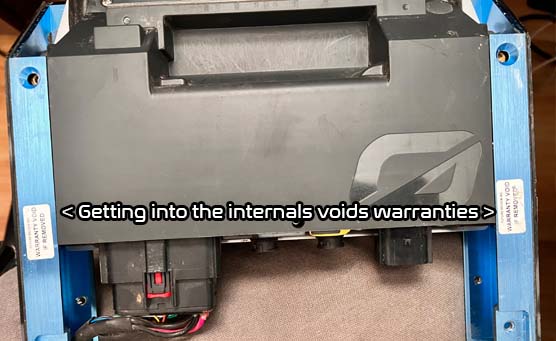
When the rider leans forward, the control system interprets this as a signal to accelerate and adjusts the motor power accordingly. Conversely, when the rider leans backward, the control system slows down or applies regenerative braking to decelerate the Onewheel.
By constantly monitoring the input from the gyroscopes and accelerometers, the control system can maintain the Onewheel’s balance by adjusting the motor output to match the rider’s movements. This enables the rider to intuitively control the speed, direction, and balance of the Onewheel.
The beauty of the Onewheel is that there are no handheld controls. It all operates on the weight of the rider. The combination of gyroscopes and accelerometers, along with the sophisticated control system, allows the Onewheel to provide a self-balancing riding experience that feels incredibly intuitive to the rider. As a rider, you sometimes feel that the Onewheel is an extension of your body because it does a terrific job responding to your movements and allocating proper motor output to keeping you stable and balanced.
The Battery Box
The Onewheel battery box houses the battery pack, Battery Management System (BMS) as well as several connections that tie this all to the controller and hub motor assembly.
The Onewheel Battery Pack
Most Onewheel battery packs consist of a series of lithium-ion battery cells connected together to form a single pack. Battery packs vary depending on model but in general, they typically contain between 15 to 20 individual battery cells.
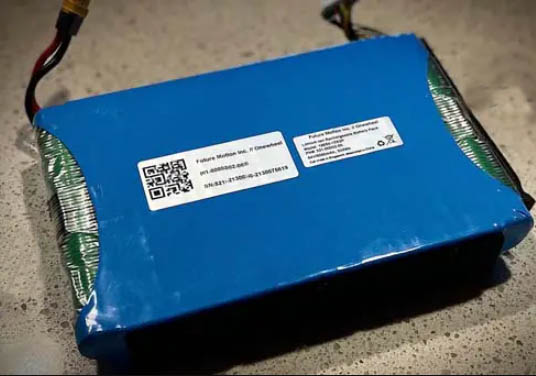
These cells are arranged in a series configuration, meaning that the positive terminal of one cell is connected to the negative terminal of the next cell, forming a continuous chain. This series connection increases the overall voltage output of the battery pack.
The voltage of each individual lithium-ion cell can vary, but commonly used cells have a nominal voltage of 3.6 to 3.7 volts. By connecting multiple cells in series, the voltage of the battery pack can reach levels suitable for powering the motor and electronics of the Onewheel.
The Onewheel BMS [Battery Management System]
The BMS or battery management system is a crucial component that ensures the safe and optimal operation of the battery pack. The BMS monitors and manages various parameters of the battery, protecting it from overcharging, over-discharging, and other potentially harmful conditions. Here’s how the BMS works in a Onewheel:
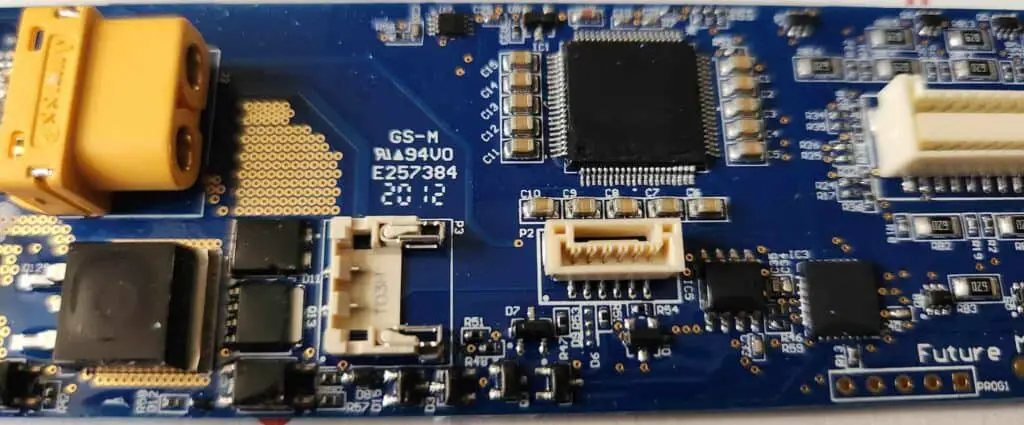
Voltage Monitoring:
The BMS continuously monitors the voltage of each individual cell within the battery pack. It ensures that the voltage of each cell remains within safe limits. If the voltage of any cell goes above or below the acceptable range, the BMS takes corrective measures to prevent damage to the battery.
The BMS also balances the voltage of the cells in the battery pack. Since individual cells may have slight variations in their voltage levels due to manufacturing tolerances or usage, the BMS equalizes the voltage across all cells by redistributing energy or managing charging/discharging rates.
Temperature Monitoring:
The BMS monitors the temperature of the battery pack to prevent overheating. Lithium-ion batteries are sensitive to high temperatures, which can degrade their performance and be somewhat of a safety risk. The BMS uses temperature sensors placed within the battery pack to measure the temperature at critical points.
If the temperature exceeds a safe threshold, the BMS may take measures such as reducing the charging/discharging rate or limiting power output to prevent overheating. Remember: The only way the board can discharge heat is through the rails. It utilizes the frame (rails of the onewheel) as a heat sink. Powdercoated rails (as seen on the GT) can limit the heat dissipation. *Some riders add ferrofluid within the hub assembly to provide added colling.
Overcurrent and Short Circuit Protection:
The BMS can detect overcurrent conditions and protect the battery pack from excessive current flow. It monitors the current going into and out of the battery pack and compares it to predefined thresholds. If an overcurrent situation is detected, the BMS can limit the current flow or shut down the system to prevent damage to the battery and other components. You may see this error code come up when excessively regenerating.
The BMS also safeguards against short circuits, which can occur if there is a direct connection between the positive and negative terminals of the battery. It detects such instances and quickly shuts down the system to prevent a potential safety hazard.
State of Charge (SOC) Calculation:
The BMS calculates the State of Charge (SOC) of the battery pack, which indicates the remaining capacity of the battery. It uses sophisticated algorithms that take into account factors such as voltage, current, temperature, and previous usage patterns to estimate the SOC accurately.
By monitoring the SOC, the BMS provides a rider with some battery information through the Onewheel app or the LED status bar on the foot pad. This allows the rider to gauge how much range is available and plan their ride accordingly.
Cell Balancing and Cell Protection:
As mentioned earlier, the BMS ensures that the voltage across all cells in the battery pack is balanced. It achieves this by managing the charging and discharging of individual cells. If a cell reaches its maximum voltage during charging, the BMS can reduce the charging rate or divert current to other cells until balance is restored.
Additionally, the BMS protects the battery from deep discharge situations that can harm the cells’ performance and longevity. It prevents the battery from discharging beyond safe limits by initiating a low-power or shutdown mode when the battery voltage reaches a critical threshold.
The BMS continuously monitors and manages these parameters in real-time, allowing the battery pack to operate safely, efficiently, and optimally. It plays a vital role in extending the lifespan of the battery, preventing damage, and providing a reliable and enjoyable riding experience with the Onewheel. You may hear about ‘zombie boards’. This means they are operating without a BMS. With all the benefits a BMS gives to the lifespan of your batteries, its not a good idea to run without a BMS. Even with the BMS, its beneficial for the battery to be left plugged in overnight once a month so that the the battery cells can completely be balanced.
Hub Assembly Unit:
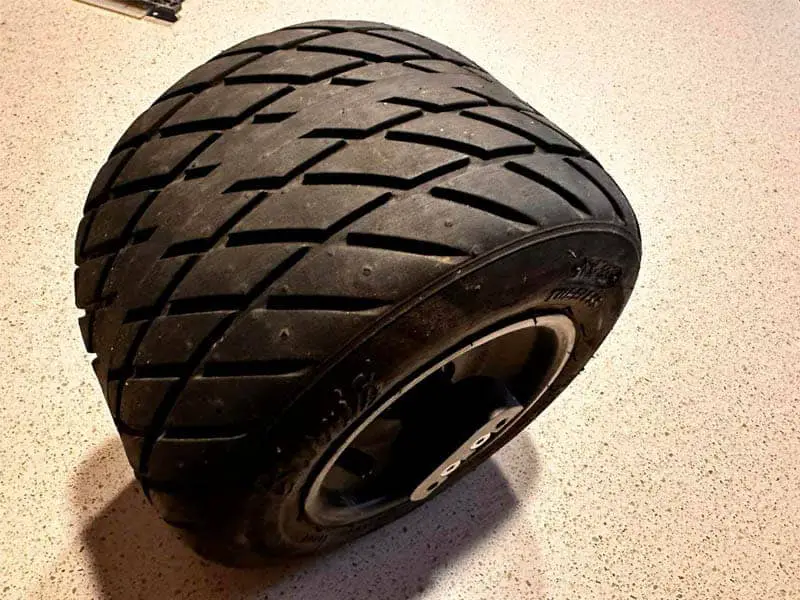
This unit is comprised of the hub, motor (stator, rotor, hall sensors) & tire.
Hall sensors play a crucial role in the operation of a Onewheel. They are used to detect the position and movement of the motor’s rotor, which is essential for maintaining balance and controlling the Onewheel’s speed.
Rotor Position Sensing:
Hall sensors are typically placed around the motor’s stator, which is the stationary part of the motor. The rotor, on the other hand, is the rotating part of the motor that is connected to the wheel. The hall sensors detect the position of the rotor as it spins around.
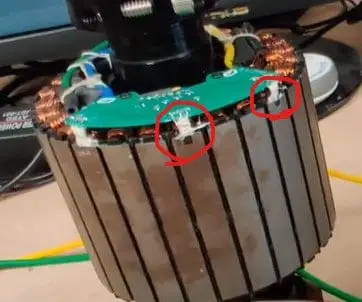
By monitoring the rotor’s position, the hall sensors provide feedback to the control system about the current position of the wheel which keeps the rider balance and stable, as it allows the control system to adjust the motor output accordingly.
Speed Control:
In addition to rotor position sensing, hall sensors also assist in controlling the speed of the Onewheel. As the rotor rotates, the hall sensors detect the passing of magnets embedded within the rotor. This provides precise information about the rotational speed of the motor.
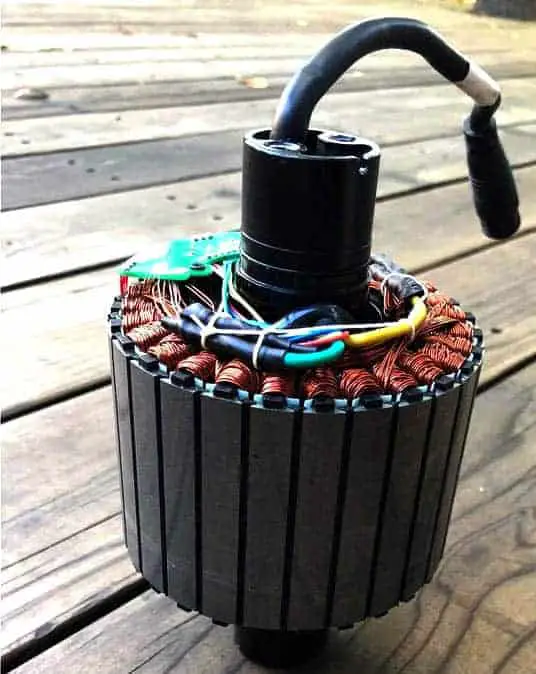
By monitoring the speed of the rotor, the hall sensors enable the control system to regulate the motor’s power output. This allows the Onewheel to maintain a consistent speed as desired by the rider. The control system can adjust the power sent to the motor based on the inputs of the hall sensors. This makes sure that the rider has a smooth ride.
Safety Features:
Hall sensors also contribute to the safety features of a Onewheel. In the event of motor failure or abnormal behavior, the hall sensors can detect any irregularities in the rotor’s position or speed. This information can be used to activate safety measures such as motor shutdown or alerting the rider about a potential issue (error code 11).
By always monitoring the rotor’s position and speed, the hall sensors provide important data to the control system so everything functions as it should.
Motor Magnets:
The magnets inside the motor of a Onewheel play a crucial role in its operation. These magnets are strategically placed within the motor assembly to generate the magnetic field necessary for the motor to function. When an electric current is passed through the motor’s coils, it creates a magnetic field. The interaction between the magnetic field generated by the magnets and the magnetic field generated by the electric current causes the motor to rotate. This rotation is what powers the movement of the Onewheel.
The magnets inside the motor are designed to have a fixed magnetic orientation, meaning they have a north and south pole that remains constant. This fixed orientation ensures that the motor rotates in a specific direction and provides the necessary torque to drive the Onewheel forward.
In addition to their role in generating motion, the magnets also contribute to the efficiency and performance of the motor. The strength and quality of the magnets can affect factors such as power output, torque, and overall motor efficiency. High-quality magnets are essential for maximizing the motor’s performance and ensuring a smooth and reliable riding experience.
The Sensor – Front Foot Pad
The sensor is a two-zoned electronic that is tucked in between the front foot pad and the grip tape. This engages the motor and activates the board. The sensor has two zones and is activated when both zones have weight on them. There are modifications to make the sensor more sensitive but for the most part, this is the on/off switch for the Onewheel.
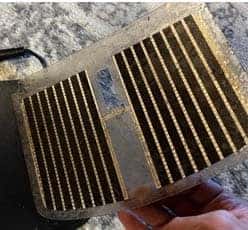
Because it is the On/Off switch for the Onewheel, when riding the board, we want to make sure the sensor stays engaged when we want it to. It’s not always perfect but the design to it is so that the board stays on so long as there is weight on at least one side of the sensor and you are traveling greater than 1 mph.
If you are traveling less than 1 mph, the Onewheel thinks you are doing a heel stop and disengages the motor.
Conclusion
The magic-like abilities of the Onewheel all start from just standing on the board. There is no hand controller. Once your foot engages the sensor, the board becomes alive. Heres the path to floating:
- Foot steps on both sides of the front foot pad (the sensor)
- Sensor engages the motor
- Motor is powered by the battery
- Motor is controlled by the accelerometers and gyroscopes
- BMS and controller constantly work in the background during the ride
- Motor stays engaged until both sides of the sensor is disengaged or 1 side of the sensor is disengaged if you are below 1mph.
- All of this is enclosed within the frame (rails) and is tied together with a wiring harness.
The controller is the main brain of the ride. Without it doing its crazy calculations, balancing that Onewheel would not be as effortless as it is. This isn’t to say that the other components are not important. They all play important roles. The BMS is always talking to the controller. Keep all of this alive by maintaining your battery and respecting your board.